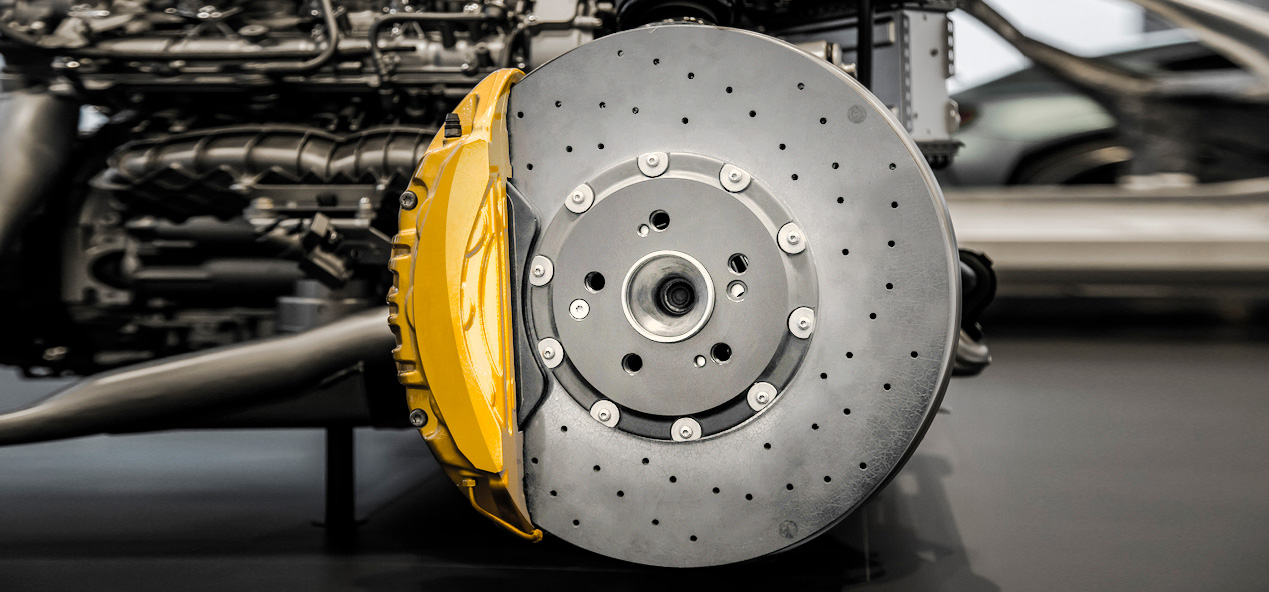
Characteristics of ceramic brake pads
Ceramic brake pads overturn the traditional concept of ceramic brake pads. Ceramic brake pads are composed of ceramic fiber, non-ferrous filler material, adhesive and a small amount of metal.
Ceramic brake pad is a kind of brake pad, many consumers will mistakenly think that it is made of ceramic at first. In fact, ceramic brake pad is based on the principle of cermet rather than non-metallic ceramic. When the brake pad is braked vigorously at high speed, high temperature will be generated on the friction surface. According to the measurement, it can reach 800-900 degrees, some even higher. At this high temperature, cermet sintering reaction will take place on the surface of the brake pad, which makes the brake pad have good stability at this temperature. However, the traditional brake pads will not produce sintering reaction at this temperature, because the sharp rise of the surface temperature will make the surface material melt or even produce air cushion, which will cause the brake performance to decrease sharply or the brake will lose completely after continuous braking.
For consultation, you can contact the Royal Automotive team and benefit from our services
Features of ceramic brake pads:
Less dust falling on wheels; long service life of disc and dual; no noise / vibration / no damage to disc. The specific performance is as follows:
(1) The biggest difference between ceramic brake pads and traditional brake pads is that there is no metal. Metal is the main friction material in the traditional brake pad, which has great braking force, but great wear and noise. After the ceramic brake pad is installed, there will be no abnormal screeching (i.e. scraping sound) during normal driving. Because there is no metal component in the ceramic brake pad, the metal clamor of friction between the traditional metal brake pad and the dual parts (that is, the brake pad and the brake disc) is avoided.
(2) Stable friction coefficient. Friction coefficient is the most important performance index of any friction material, which affects the braking ability of the brake pad. In the process of braking, due to the heat generated by friction and the increase of working temperature, the friction materials of general brake pads are affected by temperature, and the friction coefficient begins to decline. In practical application, the friction will be reduced, thus reducing the braking effect. The common brake pad friction material is not mature, and the friction coefficient is too high, which results in the unsafe factors such as out of control direction, burning of the pad, scratching of the brake disc and so on. Even when the temperature of the brake disc reaches 650 ℃, the friction coefficient of the ceramic brake pad is still about 0.45-0.55, which can ensure that the vehicle has good braking performance.
(3) The ceramic has good thermal stability, low thermal conductivity and good wear resistance. The long-term use temperature is 1000 ℃, which makes the ceramic suitable for the high-performance requirements of various high-performance brake materials, and can meet the technical requirements of high-speed, safety and high wear resistance of brake pads.
(4) It has good mechanical strength and physical properties. Able to bear large pressure and shear force. Before the friction material products are assembled and used, it is necessary to drill, assemble and other mechanical processing to make the brake pad assembly. Therefore, the friction material must have enough mechanical strength to ensure that there is no damage and fragmentation in the process of processing or use.
(5) It has very low thermal attenuation. No matter the first generation ceramic products of M09 material or the fourth generation ceramic brake pads of td58, it can still ensure that the vehicle has good braking performance to ensure safety, and the phenomenon of brake pad thermal attenuation is very small.
(6) Improve the performance of the brake pads. Because of the fast heat dissipation of ceramic materials, the friction coefficient of ceramic materials used in brake manufacturing is higher than that of metal brake pads.
(7) Security. The brake pad will produce instantaneous high temperature when braking, especially when driving at high speed or emergency braking. In the high temperature state, the friction coefficient of the friction plate will decrease, which is called thermal decay. The low thermal recession of ordinary brake pads, the high temperature state and the rise of brake oil temperature during emergency braking make the braking delay, even the safety factor of loss of braking effect low.
(8) Comfort. In the comfort index, the car owners are often most concerned about the noise of the brake pads. In fact, the noise is also a problem that ordinary brake pads have been unable to solve for a long time. The noise is caused by the abnormal friction between the friction plate and the friction plate. The causes are very complex. The brake force, brake disc temperature, vehicle speed and climatic conditions may all be the causes of the noise.
In addition, the causes of noise in the three different stages of brake initiation, brake implementation and brake release are different. If the noise frequency is between 0-550hz, it will not be felt in the car, but if it exceeds 800Hz, the car owner can obviously feel the brake noise.
(9) Excellent material properties. The high-tech materials such as large particle graphite / Brass / advanced ceramics (non asbestos) and semi metal used in ceramic brake pads have the advantages of high temperature resistance, wear resistance, brake stability, repair of damaged brake discs, environmental protection, long service life without noise, etc., overcoming the defects of traditional brake pad materials and technology is the most advanced advanced advanced ceramic brake pad in the world. In addition, the ceramic slag ball with low content and good reinforcement can also reduce the dual wear and noise of brake pads.
(10) Long service life. The service life is a very concerned index. The service life of ordinary brake pads is less than 60000 km, while that of ceramic brake pads is more than 100000 km. That’s because there are only one or two kinds of powder containing static electricity in the unique formula materials used for ceramic brake pads, and other materials are all non-static materials, so the powder will be taken away by the wind along with the movement of the vehicle, and will not adhere to the wheel hub to affect the aesthetics. The service life of ceramic material is more than 50% longer than that of common semi metal. After using ceramic brake pads, there will be no scratch (i.e. scratch) on the brake discs
Contact us for royal services and expert advice